We live in a world driven by data. The ability to harness that information for insights allows businesses to make smarter, more cost-effective decisions. In the wake of the pandemic, CEOs emphasize the need to “aggressively pursue” operational agility and flexibility over the next two to three years. However, they must adopt a new operating model to sift through the data and uncover valuable insights to optimize performance. Digitally connected assets allow businesses to facilitate remote monitoring of high-value physical equipment, resulting in a mass repository of real-time data. As detailed in “A new model for connected assets,” a recent report by the IBM Institute for Business Value, intelligent assets, machine learning, and digital twins help organizations build more resilient and efficient operations.
A new intelligent operating model
According to the study, businesses will be heavily investing in technology such as cloud, advanced analytics, automation, and the Internet of Things (IoT). Under pressure to maximize performance, companies are looking at these technologies to help streamline and transform operations for the next generation of their business. Instead of starting from the ground up, organizations can create an intelligent workflow by adding AI, machine learning, and automation to their existing systems, allowing business leaders to benefit from data insights and improve operations.
Process industries lead in connected operations
Process industries, particularly those with continuous processes such as chemicals and petroleum and oil and gas, have been adversely impacted by the volatility in the supply chain. Resilience is key in these industries due to the unpredictability of demand and uncertainty of feedstock. Because companies in these industries are typically asset intensive and intent on operational safety and stability, it is crucial they utilize their assets to the maximum potential, including production processes (like reactors or columns), physical equipment (compressors, pumps, and exchangers) or personnel executing the operations.
Sustainability in manufacturing is becoming more of a priority goal than a “good-to-have.” In process industries, cost of operations, including the cost of information management, is under scrutiny due to the push toward net zero targets, making businesses shift toward alternate and new energy options.
New technology is being adopted and leveraged for innovation in all these priority areas. This includes collecting large volumes of new information through connected assets, managing the information in the cloud, and enabling AI at scale. Metrics are being assessed to address financial (for example, EBITDA) and sustainability-focused areas (for example, worker health, emissions monitoring, asset utilization, and energy management). Understanding how each connected asset correlates to the process, whether it is engineering, design, construction, or operation, is vital. Digital representations such as digital twins play a key role in streamlining asset maintenance and adding transparency in the manufacturing space.
Being proactive with digital twins
Digital twin technology for asset maintenance can facilitate remote monitoring, predictive planning, and the proactive management of physical assets so businesses can make smarter, more efficient decisions. However, lack of access to maintenance information can make it difficult for companies to adopt digital twin technology. For example, factory equipment can come from an OEM, or original equipment manufacturer, but the OEM may not have shared all the required maintenance information. It may be contracted with the factory to come and maintain the equipment, or it might charge money to provide physical copies of maintenance documents.
These gaps can be filled by consolidating and streamlining OEM maintenance information for customers. Platforms such as IBM’s Digital Twin Exchange manage content provided by OEMs, such as service manuals and parts lists for consumer use. Customers can browse, purchase, and download digital twin information to better inform their maintenance and operations. In turn, OEMs are freed from the costs associated with managing a website to host their manuals and have another avenue for generating revenue and improving customer satisfaction.
Reducing the knowledge gap
Many businesses face a common obstacle: how to capture the institutional knowledge of the retiring baby-boomer generation that has been built over many years and transfer it to the new workforce. Baby boomer technicians came into the workforce with deep, almost intuitive, mechanical knowledge, whereas today’s technicians are coming in with less mechanical and much more digital expertise.
Technicians on average spend 80% of their time performing reactive maintenance work, much of which requires looking up information. Proactively providing them all with the information needed to do their job via a mobile device can greatly streamline the time it takes to complete a task and help improve their experiences as employees. Interactive, self-learning (improving) systems that can guide the worker and provide suggestions are part of the new employee experience.
Creating a repository of digital twin information, including lessons, insights, pictures, and videos, can help companies capture the valuable data they need for their workforce. Leveraging AI and machine learning can help to understand and sort through all the information and tie it back to the equipment to help every technician optimize performance.
Read more about how intelligent assets can optimize performance and transform business processes.
Meet the authors
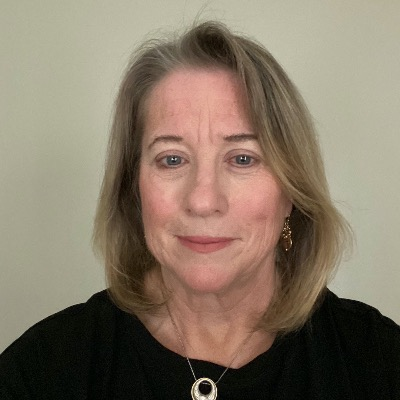