Process for working clearances
The process for working clearances involves the provision by operations of a clearance boundary to support the safe completion by maintenance of specific work activities. The process is flexible and can be adapted to suit business needs. However, the basic elements of the process are relevant to all nuclear organizations.
The following diagram illustrates the basic elements of the process flow for a single working clearance, including clearance status changes and key process steps. The diagram illustrates the collaboration between maintenance staff who identify the requirement for clearance protection, and operations staff who specify, apply, and restore the clearance boundary. Within operations, there is a distinction between operations staff in the control room who have overall responsibility for managing the clearance, and operations staff in the plant who are responsible for applying and restoring the clearance boundary in the field. The subprocess for craft involvement is optional and can be included or excluded by configuring the relevant clearance option. The options for craft involvement and other clearance features are configured separately for each site in the Organizations (Nuc) application.
The process flow diagram and the explanation of process steps that follows do not include information about the process for clearance revisions.
Figure 1. Process flow for a working clearance
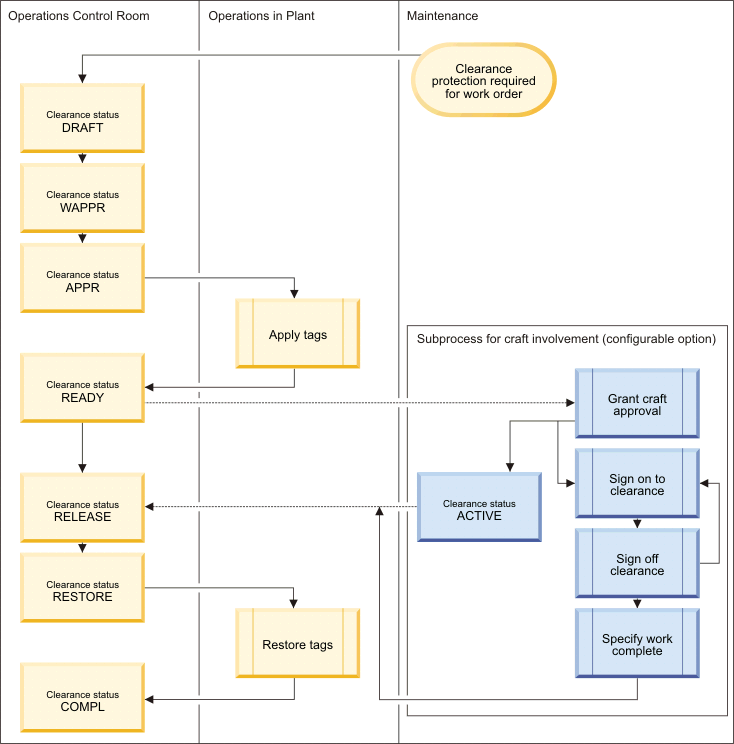
Specifying the requirement for clearance protection
In the Work Order Tracking (Nuc) application, maintenance staff specify the requirement for clearance protection on the main tab of a work order. By default, the requirement for clearance protection can be added or removed only when the work order has a status of Waiting for Approval (WAPPR) or Approved (APPR). However, you can change the default setting for the relevant clearance option if you want to modify this restriction.
Initiating the clearance
In the Clearances (Nuc) application, operations staff add the work order to an existing clearance, if a suitable match is found, or a new clearance that is created specifically to meet the new requirement. The default status for a new clearance is Draft.
On the Application tab of the clearance record, operations staff specify the components that comprise the clearance boundary by defining the required component tags. For each tag, operations staff specify the configuration details that are required for application of the clearance boundary, including the application sequence number, application position, tag type, and the requirement for independent verification. Allowable positions for each component, and the associated verification requirements, are defined on the component record. By default, verification requirements cannot be changed on the clearance record. However, you can change the default setting for the relevant clearance option to allow verification requirements to be changed on draft clearances.
The default status for tags that are defined on the clearance is Draft. The clearance might also include shared tags that were originally defined on another clearance but match the tagging requirements for boundary components on the current clearance. The use of shared tags reduces the effort that is involved in defining multiple tags for the same component.
Operations staff can manually check for potential clearance and tag conflicts before sending the clearance for approval. A tag conflict arises when conflicting tags for the same component are defined on two different clearances. Checking for potential conflicts before tags are applied reduces the risk of physical tag conflicts arising in the field.
The operations staff can also manually check for conditions that violate established requirements for single owner tags.
The tag sharing, single owner tags, and conflict checking actions are both available from the More Actions menu in the Clearances (Nuc) application.
While the clearance is in draft status, operations staff can specify restoration details for some or all boundary components. However, the specification of restoration details in the early stages of the clearance life cycle is optional. Restoration details are not required until the clearance is due for release following the completion of work by maintenance staff.
Approving clearance application
When all required tags are defined, a Tagging Official approves the clearance to confirm that it provides a safe boundary for the scope of protected work. When a clearance is approved by the Tagging Official, the clearance status is changed to Waiting for Approval (WAPPR). The clearance boundary and the scope of protected work cannot be changed unless a Shift Supervisor rolls the status of the clearance back to Draft.
The clearance must also be approved for application by a Shift Supervisor. Shift Supervisor approval changes the clearance status from Waiting for Approval to Approved. The Shift Supervisor approval action can be configured to include an automatic conflict check and a tag sharing proposal. These functions provide the Shift Supervisor with an opportunity to align tags on the current clearance with tags that are planned elsewhere or already applied in the field. In the Organizations (Nuc) application, you can change the default settings to specify different conflict checking and tag sharing options for the process of Shift Supervisor approval at each site.
The Tagging Official and Shift Supervisor application approval actions are both available from the More Actions menu in the Clearances (Nuc) application.
Applying and verifying tags
When the status of the clearance is changed to Approved, physical tags can be printed. Operations staff position the boundary components and hang the physical tags to make clearance configuration details visible to workers in the field. Where necessary, component positions are independently verified: components cannot be positioned and verified by the same person.
After tags are hung, operations staff update the clearance record with applier details. Operations staff must also add verifier details for components that require independent verification. The addition of applier details changes the status of individual tags to Applied. The addition of required verifier details does not affect tag status but it is a prerequisite for changing clearance status. For components that do not require independent verification, operations staff can add verifier details on an optional basis.
Applier and verifier details can be added to the clearance record in the Clearances (Nuc) application or the Clearances Kiosk (Nuc) application. The Clearances Kiosk (Nuc) application supports the entry of applier and verifier details by different users within the same Maximo® session.
Changing the clearance status to Ready
When the clearance record includes applier details for all tags, and verifier details where required, operations staff manually change the status of the clearance to Ready. This status change can also be automated by configuring the relevant clearance option at the site level.
The configuration of the clearance option for craft approval determines whether a clearance with a status of Ready enters the subprocess for craft involvement. If craft approval is required, the clearance enters the subprocess for craft involvement. During this subprocess, maintenance assume temporary control of the clearance and use the associated work orders to approve, sign on to, and ultimately release the clearance back to operations.
If craft approval is not required, the clearance remains in a status of Ready while maintenance users work in the protected workspace. The option to sign on to and off the clearance is not available.
The clearance option for craft approval can be configured differently for each site.
Subprocess for craft involvement
The subprocess for craft involvement includes the following steps:
- Maintenance staff grant craft approval in each of the associated work orders to confirm that the clearance provides adequate protection for all work order tasks. When craft approval is first granted in any of the associated work orders, the status of the clearance is automatically changed to Active. This status change signifies that work in the protected workspace can begin. During craft approval, component tags are copied from the clearance to the associated work order. A configurable clearance option determines whether the craft approver must manually select the individual tags that are relevant to the work order, or whether all tags on the clearance are automatically added. Typically, craft approval is performed by a maintenance supervisor.
- Maintenance staff can provide multiple craft approvals in the same work order for the same clearance revision. Only the first craft approval changes the clearance status to Active.
- While the clearance is in Active status, maintenance staff sign on to and off the clearance to register work that is being performed under clearance protection. The last maintenance user to sign off the clearance specifies that work under clearance protection is complete.
- Work orders that enter the craft involvement subprocess through craft approval must be released from the clearance before clearance restoration. Work orders are automatically released when the last maintenance user signs off the clearance and specifies that work is complete. Work orders can also be manually released in the Work Order Tracking (Nuc) application provided that all maintenance users have signed off. Typically, manual release is performed by a maintenance supervisor. The release of a work order for which craft approval exists is a prerequisite for work order completion and for changing the status of the clearance to Approved for Release (RELEASE).
Preparing for clearance restoration
Restoration details can be added to or changed on a clearance that has a status of Draft, Waiting for Approval, Approved, Ready, or Active. Operations staff can manually specify restoration positions for each component, or use the generate restoration function to automate the proposal of default restoration positions that are associated with a particular restoration condition. The positions that are available for manual selection are defined on the component record. The default restoration positions that are obtained during generation originate either on the component record or on an active lineup plan.
Operations staff can manually check for potential tag restoration conflicts before the clearance is approved for restoration. A restoration tag conflict occurs when conflicting application or restoration positions for the same component are defined on two different clearances.
Approving clearance release
Clearance restoration is initiated when a Tagging Official approves the release of the clearance. The following prerequisites apply:
- All work orders associated with the clearance are released from the clearance by maintenance staff, or have never had craft approval.
- Restoration details, including the restoration sequence number, restoration position, and the requirement for independent verification, are specified for all tags on the clearance that are not shared. Shared tags represent components that are still in use as boundary components on at least one other clearance and, for this reason, cannot be restored.
Tagging Official release approval changes the status of the clearance to Approved for Release. The action also changes the status of tags that qualify for restoration in the current clearance to Pending. When the clearance is approved for release, the restoration sequence numbers and positions can no longer be changed.
Approving clearance restoration
By default, following Tagging Official release approval, the clearance must be approved for restoration by a senior reactor operator. This approval action changes the clearance status to Approved for Restoration (RESTORE). However, you can change the default setting for the relevant clearance option to bypass Shift Supervisor restoration approval and automate this status change.
The Shift Supervisor approval action for clearance restoration can be configured to include an automatic conflict check.
Restoring and verifying tags
When the clearance status is changed to Approved for Restoration, operations staff remove tags and then restore the boundary components in the field to the restoration positions that are specified on the clearance. The requirements for independent verification of specific component positions are fulfilled; components cannot be repositioned and verified by the same person.
For each component that is restored, operations staff update the clearance record with restorer details. Operations staff must also add verifier details for components that require independent verification. The addition of restorer details changes the status of individual tags to Restored. The addition of required verifier details does not affect tag status but it is a prerequisite for changing clearance status. For components that do not require independent verification, operations staff can add verifier details on an optional basis.
Restorer and verifier details can be added to the clearance record in the Clearances (Nuc) application or the Clearances Kiosk (Nuc) application.
Completing and closing the clearance
When the clearance record includes restorer details for all tags, and verifier details where required, the status of the clearance is automatically changed to Completed (COMP). If the clearance includes any shared tags, and all other tags include restorer details and verifier details where required, the clearance status is automatically changed to Waiting for Shared Tags (WHSARE). When the shared tags are restored and verified on the last sharing clearance, the status of the current clearance is automatically changed to Completed.
Following final review, operations staff change the status of the clearance to Closed. The closed clearance, and any previous clearance revisions, are stored as history records that cannot be modified.